Product Description
Hot blast stove used silica fire resistant refractory brick

Silica bricks consist of > 90 percent by weight of SiO2. In general, the SiO2 content is 95 to 97% weight.
silica fire resistant refractory brick with a SiO2 content of ≥ 95 % are manufactured from selected pure, well washed, crushed and carefully mixed quartz raw materials. These materials are obtained mainly from our own quarzite deposits.
The operating equipment and the operating procedures guarantee manufacture of silica bricks with excellent stability, defined mineralogical compositon and high stability under high temperature and pressure stresses. The main areas of use for silica bricks are coke oven plants (oven floor, heating wall, oven roof and the upper regenerator layers), the superstructure of glass melters (and where required also in the upper structure of the regenerator) and in the high temperature areas of hot blast stoves.
Brick types for particularly high demands in glass melters are manufactured by carefully selected offset components and special manufacturing processes. Low flux silica bricks, low lime bricks and lime free bricks form part of this category.
Product Uses
Application of Hot blast stove used silica fire resistant refractory brick
1,Coke oven
2,Hot blast stove
3,Glass tank
4,Other industrial kilns
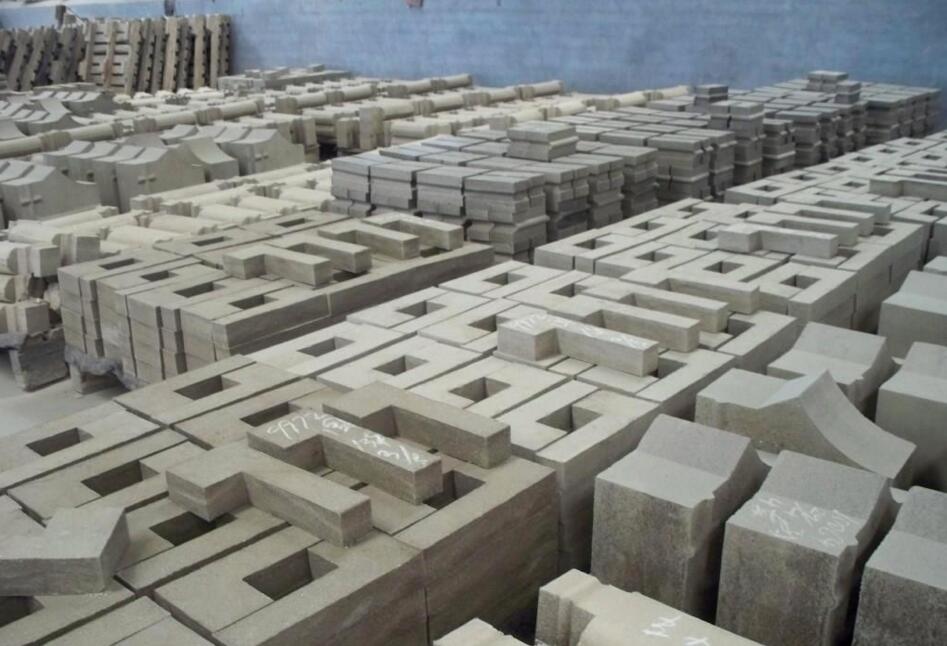
Advantages
silica fire resistant refractory brick, accurate size , neat appearance ; phase composition to phosphorus-based quartz, square quartz supplement, high bulk density, thermal conductivity, high temperature creep stability, long-term use is not Deformation. coke oven silicon brick life has been more than 20 years (in using).
1,high density, good thermal conductivity
2,High RUL
3,High tridymite
4,Low true density
5,Low expansion
6,Low creep
7,Residual quartz content
8,Accurate size, pure color and good appearance.
Technology
Chemical and physical index of Hot blast stove used silica fire resistant refractory brick
Item | ZS-94 | ZS-95 | ZS-96A | ZS-96B |
Chemical composition% | SiO2 | ≥94 | ≥95 | ≥96 | ≥96 |
| Fe2O3 | ≤1.5 | ≤1.5 | ≤0.8 | ≤0.7 |
| Al2O3+TiO2+R2O | | ≤1.0 | ≤0.5 | ≤0.7 |
Refractoriness ℃ | 1710 | 1710 | 1710 | 1710 |
Apparent Porosity% | ≤22 | ≤21 | ≤21 | ≤21 |
Bulk Density g/cm3 | ≥1.8 | ≥1.8 | ≥1.87 | ≥1.8 |
True Density, g/cm3 | ≤2.38 | ≤2.38 | ≤2.34 | ≤2.34 |
Cold Crushing Strength Mpa | ≥24.5 | ≥29.4 | ≥35 | ≥35 |
Refractoriness Under Load T0.6 ℃,0.2Mpa | ≥1630 | ≥1650 | ≥1680 | ≥1680 |
Permanent Linear Change On Reheating (%)1500℃X2h | 0~+0.3 | 0~+0.3 | 0~+0.3 | 0~+0.3 |
20-1000℃ Thermal Expansion 10-6/℃ | 1.25 | 1.25 | 1.25 | 1.25 |
Thermal Conductivity (W/MK) 1000℃ | 1.74 | 1.74 | 1.44 | 1.44 |
Packaging & Shipping
Packaging of Hot blast stove used silica fire resistant refractory brick
1.on wooden pallets with plastic cover: wooden pallet size :930*930 or 1000*1000mm,
2.Load weight of each pallet: 1.5-2.0 tons,
3.230*114*65mm:512PCS/Pallet, 230*114*75mm:448PCS/Pallet.
Shipping of Hot blast stove used silica fire resistant refractory brick
1.Our packaging is as per customer’s request
2.Normal goods delivered by sea transport
3.Sample shipping by express
4.We will shipping and delivery goods timely, quanlity and quantity guaranteed, and also in accordance with the contract and customer's requirment completely.
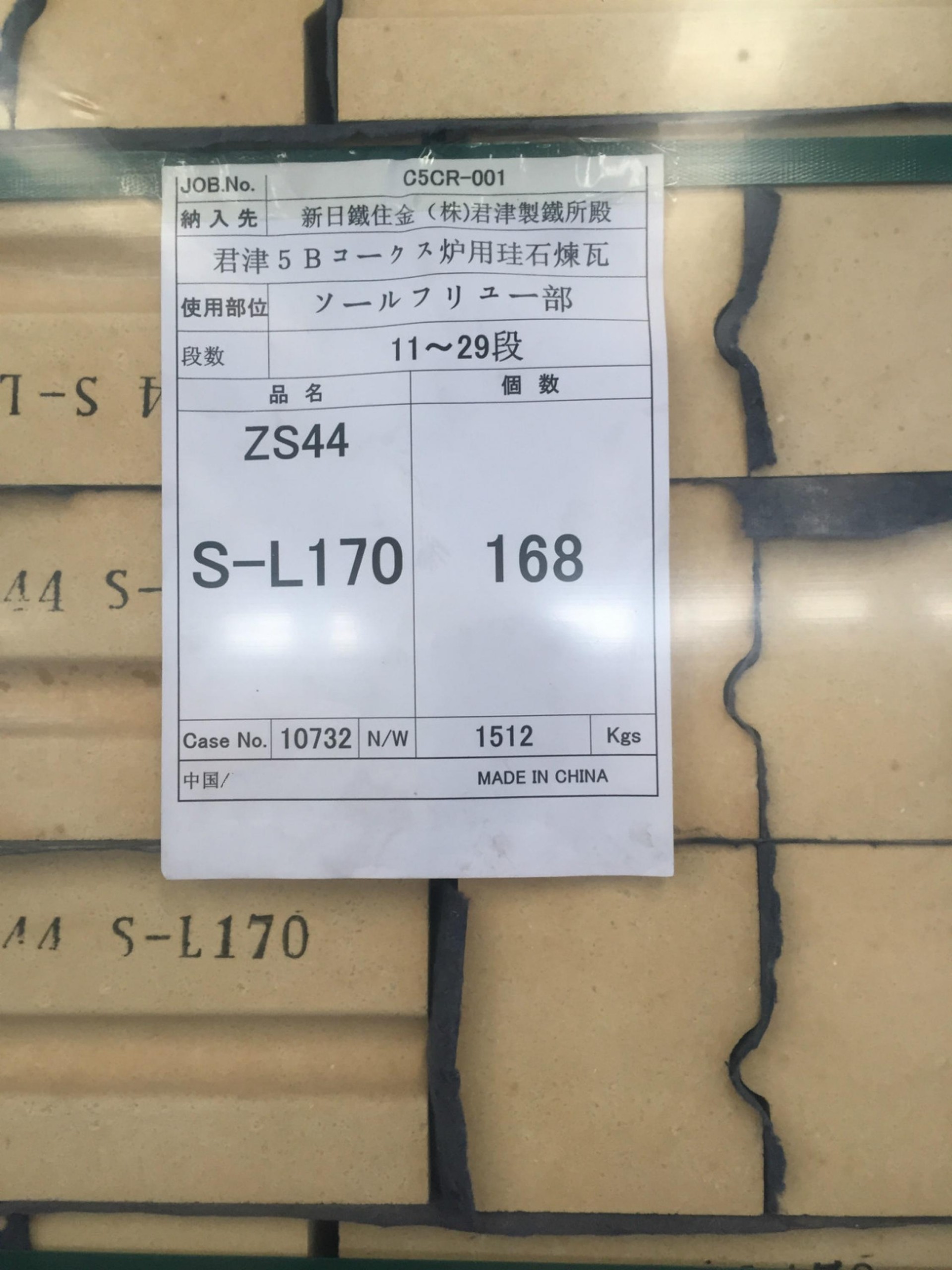

Why choose Us

1. Strong professional:
Our company has thirty years producing experience in refractory product. Our manager will supervise on a various refractory' s production materials, process control, quality supervision and package delivery, and ensure the products are 100% qualified.
2. Production equipment:
Production and testing equipments are new, complete and automated or semi- automated. Such modern facilities and equipments have provided the fine technical guarantee for the production and testing.
3. Testing equipment;
Our company's testing equipments as follows:
High Temperature RUL Tester
Bulk Density Tester
The Pressure Tester
Refractoriness Tester

